Over the summer, four students at KAIST Idea Factory embarked on a journey to improve the current 3D printers. Their success was to be celebrated four months later, at the launching event of their very own ‘Neuron’ – a 3D printer remedying the shortcomings of existing 3D printers. The KAIST Herald met with the very students who created ‘Neuron,’ namely Sukhyun Seo, Seung Hwan Lim (Computer Engineering ’12), Seong Hyeon Jo (Mechanical Engineering ’12), Won Hoe Kim and Jong Hoon Choe (Mechanical Engineering ’13)
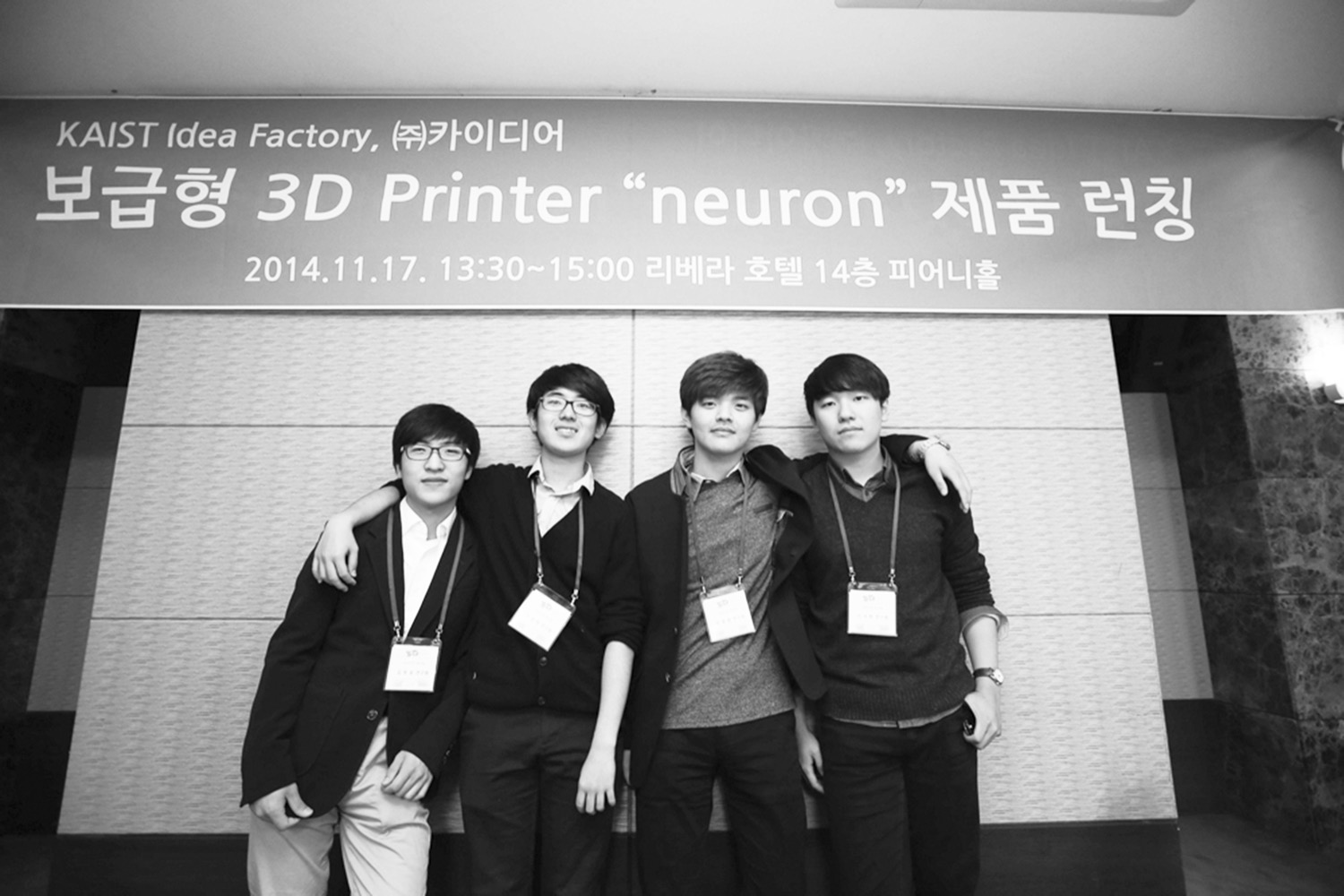
Please introduce your project.
The product we have created is a low-cost, delta-type 3D printer named ‘Neuron.’ It is a third of the price of existing 3D printers while maintaining a high performance level. It is also much user-friendly than other predecessors.
How did the idea for the ‘Neuron’ come about?
Our team members were initially involved in different projects at Ideafactory, a part of the Research Institute for Social Technology and Innovations (RISTI). While creating prototypes with 3D printers, we came across some setbacks of the existing 3D printers available, such as the difficulty in usage as well as other functional shortcomings. This is when we gathered to improve the very tool that we had been using.
How is the ‘Neuron’ different from the existing 3D printers?
Firstly, ‘Neuron’ has a very low price tag (under 1 million Won) while still being equipped with the auto levelling technology. This function allows the surface to be leveled automatically while printing and thus increases convenience. Secondly, the 3D designing interface has been customized as well, to make it easier for the first-timers to design their own models and other printables. We are also in the process of developing an app that makes the designing process much more user friendly. Lastly, we believe that our printer has a better, evolved design than other predecessors. We also incorporated a 3D printing technique that is rare in Korea.
How did you manage to lower the prices so significantly?
Normally, you would usually have to purchase aluminum parts that are needed in production, which would raise the production costs greatly. However, we 3D printed some of the parts that were used in ‘Neuron’ as well as created some parts, such as the extruder, ourselves. These efforts contributed to the lowering of our production costs.
What were some difficulties you faced when developing the ‘Neuron’?
Instead of the widely used Mendel Technique that moved according to and restricted to x, y and z coordinates, we incorporated the Delta Technique that allows for freer movement with three supports. This technique is rare in Korea and we faced difficulties in obtaining information about this technology. We also did not have real examples to refer to. Also, we underwent a long trial-and-error process with the extruder, which is where the printing happens. We made the extruder by ourselves from scratch, and we had to retest the whole printer countless times whenever modifications were made to other smaller parts.
What are the current status and future plans of ‘Neuron’ and the company?
We have currently finished the technology development and there is another company that would be in charge of the mass production process for us. With them, we have a company named ‘KAIDEA’. We held the launching event of ‘Neuron’ on 17 November 2014. The president Kang Sung Mo of KAIST and President Park Han-il of Korea Maritime and Ocean University as well as the vice president of Korea 3D Printing Association attended the event along with many other invited guests and press. We had the privilege of introducing ‘Neuron’ and what our vision and direction are. Currently there has been more than 100 printers on pre-orders. After hearing about ‘Neuron’ on the news, buyers and even individuals have expressed interest in placing orders. We aim to finish the production process mid-end December and start distributing the pre-ordered printers as early as mid-January. After these processes stabilize, we will start to innovate 3D printers again. Any enquiries on orders can be made to ckra333@naver.com.