As interest in implantable electronics, wearable devices, and soft robotics increases, scientists have been conducting research on elastic printed circuit boards (E-PCB). There have been multiple attempts to construct a flexible PCB. However, problems such as low electric conductivity, inelasticity, and variable electrical resistance arose. To overcome these limitations, a research team led by Professor Jihyung Kang from the Department of Materials Science and Engineering proposed an unprecedented method of manufacturing a conductive liquid metal particle network (LMPNet) in polymers to implement in the PCB. This research was selected as the cover page of the international journal Science on November 11 under the title “Universal Assembly of Liquid Metal Particles in Polymers Enables Elastic Printed Circuit Board”.
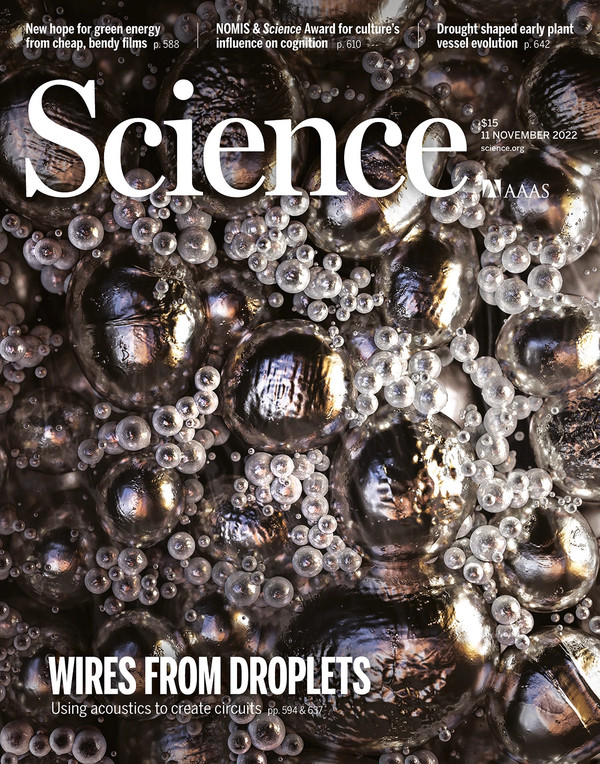
Liquid metal has always been under the attention of scientists due to its unique solid and liquid features. It is in the form of a liquid at room temperature, and is evaluated as a material suitable for use in stretchable electronic devices due to its deformability and high electrical conductivity. However, the repulsion between the liquid metal particles (LMPs) when forming a polymer was a critical drawback for E-PCB application, since the current flow was hindered. To solve this problem, the research team formed a conductive network by bridging the LMPs with nano LMPs established by applying an acoustic field, thereby developing an electrode that does not change in resistance when stretched. The results showed that the PCB could be freely deformed like rubber (to a length more than five times as long as the initial).
The research team confirmed that applying intense acoustic waves to the solution consisting of liquid metal eutectic gallium indium and thermoplastic elastomer polyurethane forms nano LMPs at the interface of polymers and creates a conductive network. The network shows low electrical resistance similar to that of copper used for the conventional PCBs, and the resistance change is negligible even when the network was elongated 10 times. In addition, due to its excellent mechanical properties, the composite has high resistance to external physical shocks. In particular, this study solved the problem of liquid metal leakage by using a non-destructive method, the acoustic fields, unlike previous physical methods such as external mechanical force application or laser sintering, which damaged the network. Through this new method, high bonding strength with various electronic components was obtained.
Based on the excellent electrical and mechanical properties and high bonding strength of the liquid metal particle network, the team suggested that the developed E-PCB could be applied to various flexible wearable electronic devices by patterning the liquid metal particle network on a stretchable polymer substrate and connecting it with electronic components. More specifically, the research team looks forward to applying the liquid metal particle networks to the synthesis of photoresist, hydrogel, and self-healing polymers as well as in high-resolution optical patterning, low impedance, body-inserted electronic devices and self-healing liquid metal-based electrodes.